ものづくり系サークルに所属する学生のために,自動車業界の国際規格IATF16949をベースとしたVDA FMEA(PFMEA)についての説明を行う
はじめに
この記事では,ものづくり系サークルに所属する学生のために,自動車業界の国際規格IATF16949をベースとしたVDA FMEA(Verband der Automobilindustrie Failure Mode and Effective Analysis)のうち、PFMEAについての説明を行う
参考文献はこれ(神の書)
↓これ以外の参考文献はここから
なお,FMEAにはスプレッドシートを用いるAIAG( Automotive Industry Action Group: 全米自動車産業協会)の流派とStructure treeを用いるVDA(Verband der Automobilindustrie: ドイツ自動車工業会)の流派があるが,この記事ではVDA FMEAを軸に説明を行う
FMEAのメリット
FMEAとは「Failure Mode and Effects Analysis」の略で,設計の段階で製品のリスクを分析し,対策を取るための手法である
↓FMEAの概要についてはここら辺の記事を参照
≫FMEAとは(AIAG&VDA - FMEA)
≫新しいFMEA-AIAG&VDA(故障モード影響解析)の作成手順を徹底解説
上記を踏まえたうえで,筆者が思う「ものづくり系サークルでFMEAを導入するメリット」を紹介する
- 自分が設計したものに対して体系的かつ網羅的にリスク分析ができる
- チームでリスクを洗い出し,原因を考え,対策を取ることができる
- 製品設計・工程設計の知見をチーム内に蓄積することができる
1. 体系的かつ網羅的なリスク分析
FMEAを実施することによって,自分が設計したものに対して体系的かつ網羅的にリスク分析ができるようになる
一般的な学生が自分で何かを設計する際は,これまで勉強してきた知識や製作の経験に基づいて「ここはやばそう」と感じる箇所について対策を取っていくことになるが、この方法では必然的に「自分の経験から重要だと感じたところ」や「ここ数年で失敗したこと」のみに対策が偏ってしまい、本当に見落としなく重大なリスクの対策できているのかを確認することができない
結果、自分の検討の甘さや勘違いなどから思いもよらない箇所で故障が発生し、それの対策にてんやわんやする羽目になってしまう
今回紹介するVDA FMEAは7つのステップで構成され、そのうちの2、3、4ステップ目でそれぞれ「Structure tree」「Function tree」「Failure tree」と呼ばれるツリーを作成し、製品の構成、構成品の機能、故障モードを整理する
ツリー形式で作成するので抜け漏れがあれば一目瞭然であり、それぞれの構成品の機能や故障モードの関連性も非常に捉えやすい。FMEAで最も困難な「故障モードの列挙」という作業も、後述する「Failure Chain」の考え方を用いることである程度論理的にこなすことができるようになる
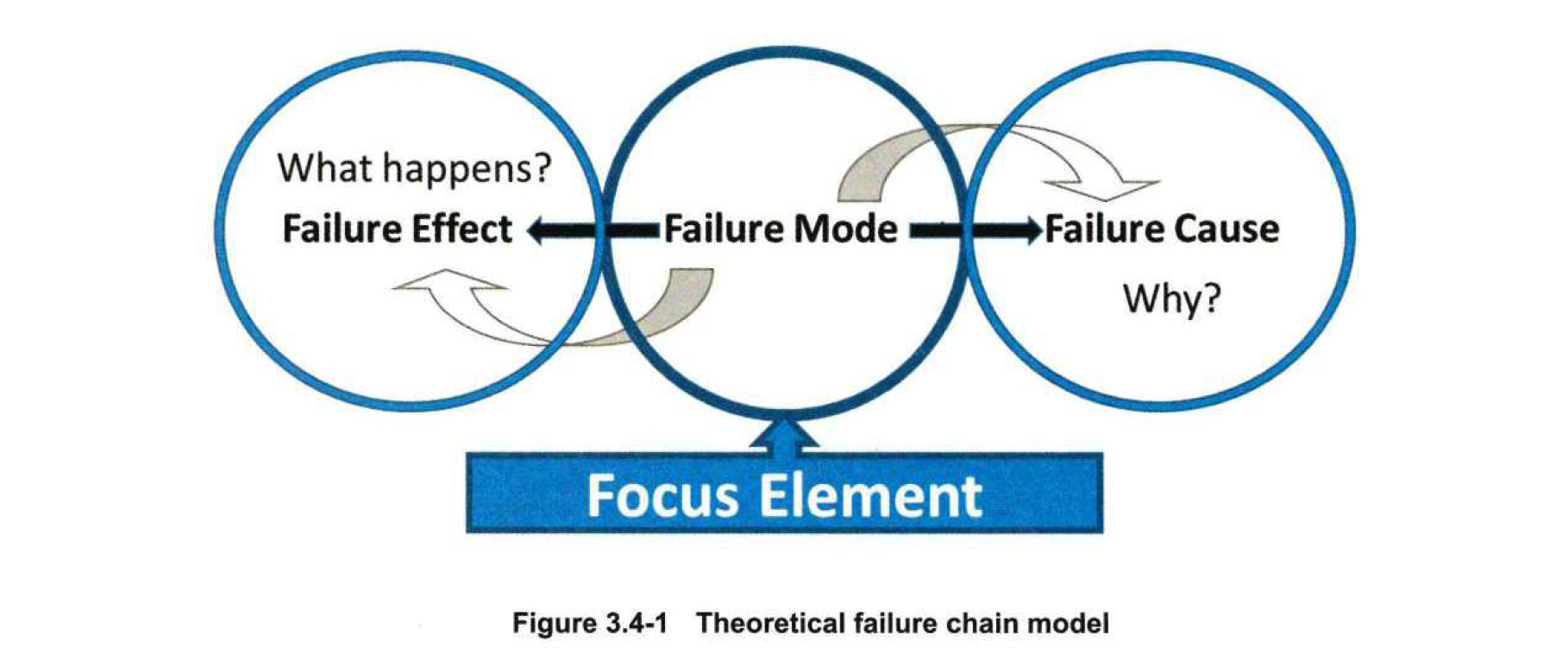
VDA FMEAを実施することで、これまでなんとなくでやって、ちゃんとできているかもよくわからなかったリスク分析/対策の作業を、網羅的かつ効率的な作業へと昇華させることができる
2. チームでの原因を分析および対策
FMEAは個人ではなくチームで行う作業だと規定されている
製品設計者あるいは工程設計者が実施したFMEAをベースとして、チームのあらゆる部門の責任者が集まってレビューを行い、FMEAを完成させていく
そんなFMEAを効果的に実施するためには様々なバックグラウンドを持ったメンバーで構成されたチーム(cross sectional team)が不可欠である
ものづくり系サークルでFMEAを実施するなら、少なくとも各セクションの代表は集まるといい
設計者以外の目線からもFMEAを実施することでリスク分析の網羅性はより盤石なものになると同時に、チーム内のステークホルダー達に製品や工程の構成、機能、故障モードを周知することができる
チームでものづくりをする上で最も重要で、かつスケジュールの都合上最もうやむやになりがちな「情報共有」という作業も、FMEAを実施することで自然と達成できることになる
また、引き継ぎも兼ねるならついでに後輩も巻き込んでしまえばいいし、設計変更や新規設計をやる場合は現役で作ったFMEAをOBに見てもらったりしてもいいかもしれない
1人では気づかないようなミスも、チームで集まり意見を交わせばどこかで防ぐことができるようになるはずである。スイスチーズモデルを有効的に活用していきたい
3. 最強の引継ぎ資料
FMEAを実施することで
- 製品/工程がどのような構成になっていて
- それぞれどのような機能を持つように意図されていて
- 故障が発生する原因と発生した際の影響が網羅されており
- それらの故障に対して定量的なリスク評価と対策の優先度が設定されており
- リスクを低減するためにどのような対策がとられたか
が、視覚的にわかりやすい形でドキュメントとして残ることになる
ものづくりを経験したことがある人なら、上記のような引き継ぎ資料を作ることがどれほど大変かが理解できると思う
FMEAはリスク分析のための優れたツールであるだけでなく、ものづくり系サークルにとって最も重要な「いまはもういない設計者の意図」を残すツールにもなる
数年でチームメンバーが全員入れ替わってしまうようなものづくり系サークルにとって、理想の引き継ぎ資料となるのではないだろうか
製品設計の引き継ぎをしたい場合はDFMEA、工程設計の引き継ぎをしたい場合はPFNEAを行えばよい
PFMEAの手順
AIAG&VDA FMEAハンドブックでは、FMEAは7つのステップで実施するよう規定されている
- Planning and Preparation
- Structure Analysis
- Function Analysis
- Failure Analysis
- Risk Analysis
- Optimization
- Results Documentation
この記事では、それぞれのSTEPについて具体的に説明していく
また,各STEPでは、筆者が設計した鳥コン滑空機であるQX-20を例にして実施手順について説明していく
↓使用したファイルのダウンロードはこちら
FMEA Tools
FMEAを実施するためには何かしらのソフトウェアがあった方がいい
スプレッドシートなどでもできなくはないが、バージョン管理や構造の把握に難があるので、今回はネットで適当に見つけた無料ツールの中からFMEA用のExcelアドインであるFMEAstudioを使うことにする
ちなみに無料版は12回までしか要素の追加ができないため、構成要素の多いFMEAを実施する場合はファイルを細かく分割する必要がある
FMEAに使えるソフトウェアは他にも種類があるし、学生であれば有料版の機能をタダで使えるものもあるかもしれないので、気にいるソフトがあるかどうか探してみて欲しい
STEP1: Planning and Preparetion
STEP1では以下のことを実施する
- BOMの作成
- PFMEAの対象の決定
BOMとは、Bill of Materialの略称で、日本語では部品表と呼ばれたりする
BOMを見れば機体を構成する全ての部品を把握できるし、これから何を作らなければならないかも認識できる
ある程度のBOMが完成したら、BOMを見ながら「どの部品に対して、どの階層でPFMEAを実施するか」を決定する
PFMEAの対象部品と階層が決まればSTEP1は完了である
例: QX-20
BOMの形式はいろいろあるが、筆者はマインドマップのツールを使ったツリー形式のBOMをおすすめする
実際にQX-20でBOMを作成してみるとこんな感じになった(クリックで拡大)
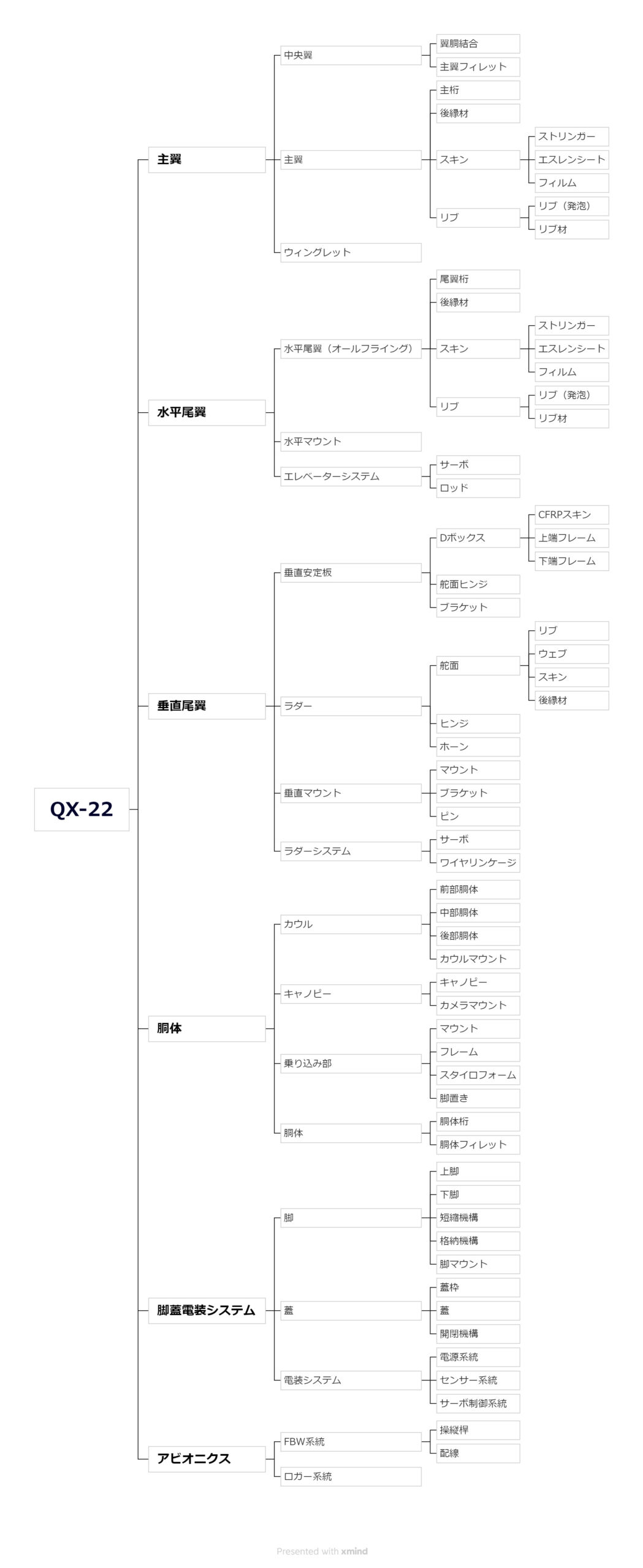
今回のBOMは全体設計の立場から作成したため階層はそこまで深くなっていないが、きちんと作成すればネジの1本まで書き下すことができる
そのレベルまで作り込まれたBOMがあるだけで、設計資料としての価値は計り知れないと思う
また、一度BOMを作りこんでしまえば、翌年以降は変更点を管理するだけでよい
この記事では例として主翼の製作工程に対してPFMEAを実施することにする
MindMeister
- オンラインで使えるマインドマップツール
- PCのブラウザとスマホアプリから同時編集が可能
- 無料版は3つまでマインドマップを作成可能
- 画像出力には非対応
Xmind
- デスクトップアプリとして使える
- ファイルはローカル保存
- ファイル数に制限なし
- 無料版で画像出力に対応
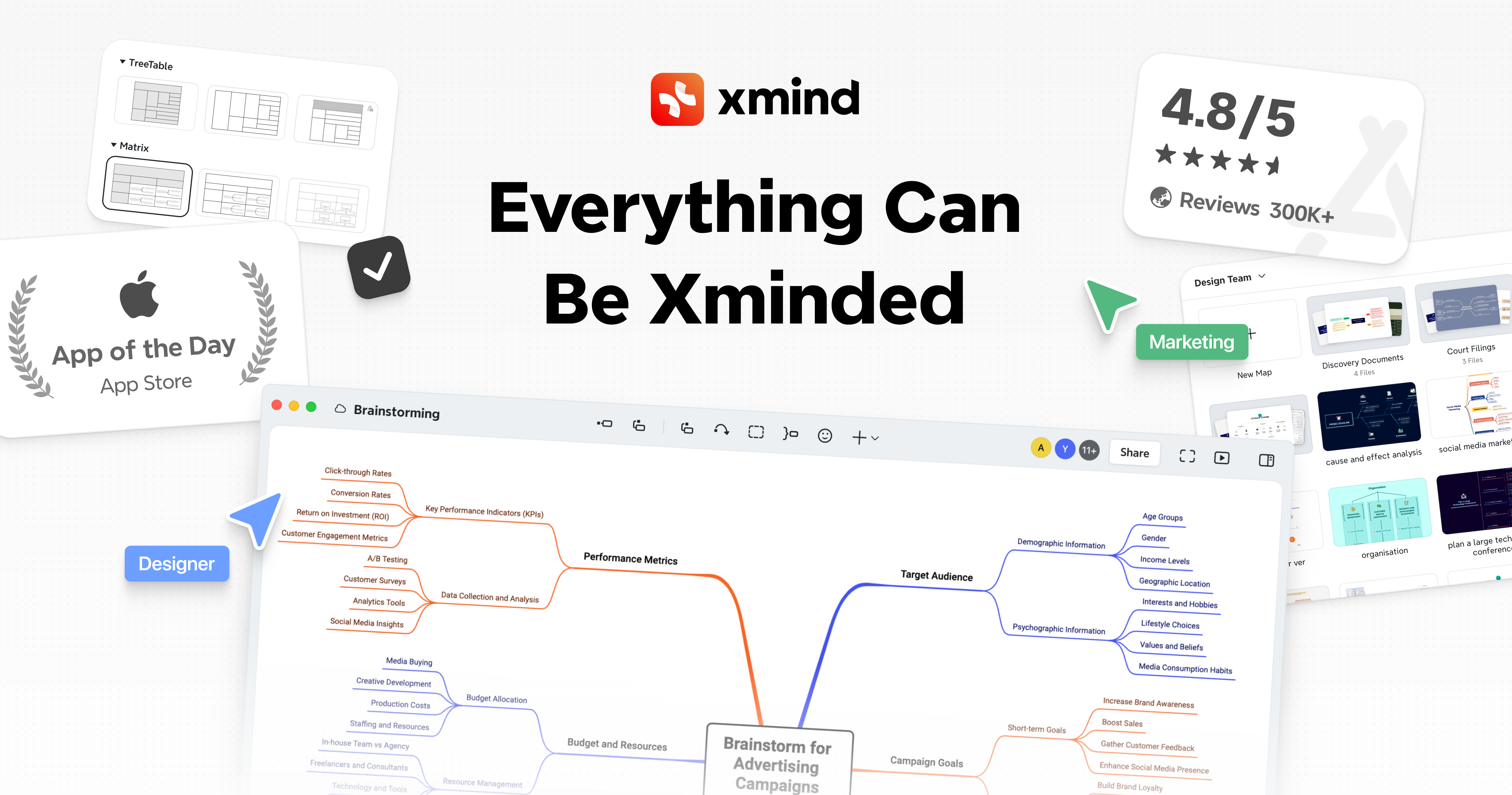
今回は画像出力ができるという点からXmindを使用している
STEP2: Structure Analysis
STEP 2では,以下のことを実施する
- Process Flowの作成
- Structure treeの作成
Process Flowの作成
Process Flowとは文字通り工程の流れであり、製品を作るために必要な工程や順番を示すものである
AIAG&VDA HandbookではPFD(Process Flow Diagram)と呼ばれるチャートのようなものを作ることになっているが、工程の流れが分かりやすく示されていれば形式は何でもよいと思う
ここで作成したProcess Flowをインプットとして、Structure treeを作成していく
Structure treeの作成
Structure treeとは,工程を構成する要素を階層的に表し,構造的なつながりによる依存関係を可視化したものである
PFMEAでは、工程を構成する要素は階層ごとに以下の3つに分類される
Process Item | 工程がすべて問題なく完了したときに得られる結果 |
Process Steps | 製造工程(OP: Operation)、PFMEAの解析の対象 |
Process Elements | 製造工程に影響を与えうる要素(4M, 5M+E, 6Mなど) |
例えばある部品の組み立て工程だと、Process Itemは工程の最終的な結果として得られる「部品の組み立て」であり、Process Stepは部品を組み立てる際の各工程である「部品をねじで固定する」「配線を接続する」とかになる
Process Elementsの概念は少しわかりにくいが、それぞれの製造工程に影響を与えうる「作業者」「作業方法」「使う治工具」「材料」「作業環境」「検査方法」「マネジメント」などの要因である
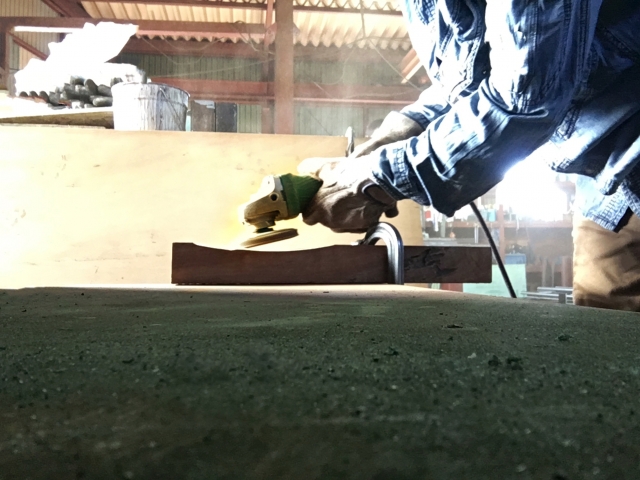
PFMEAの対象工程に対して、Process Item、Process Steps、Process Elementsの3つの階層からなるStructual treeが完成すればSTEP2は完了である
例: QX-20
Process Flow
ひとまず、主翼の製作工程をツリー形式で表現した(クリックして拡大)
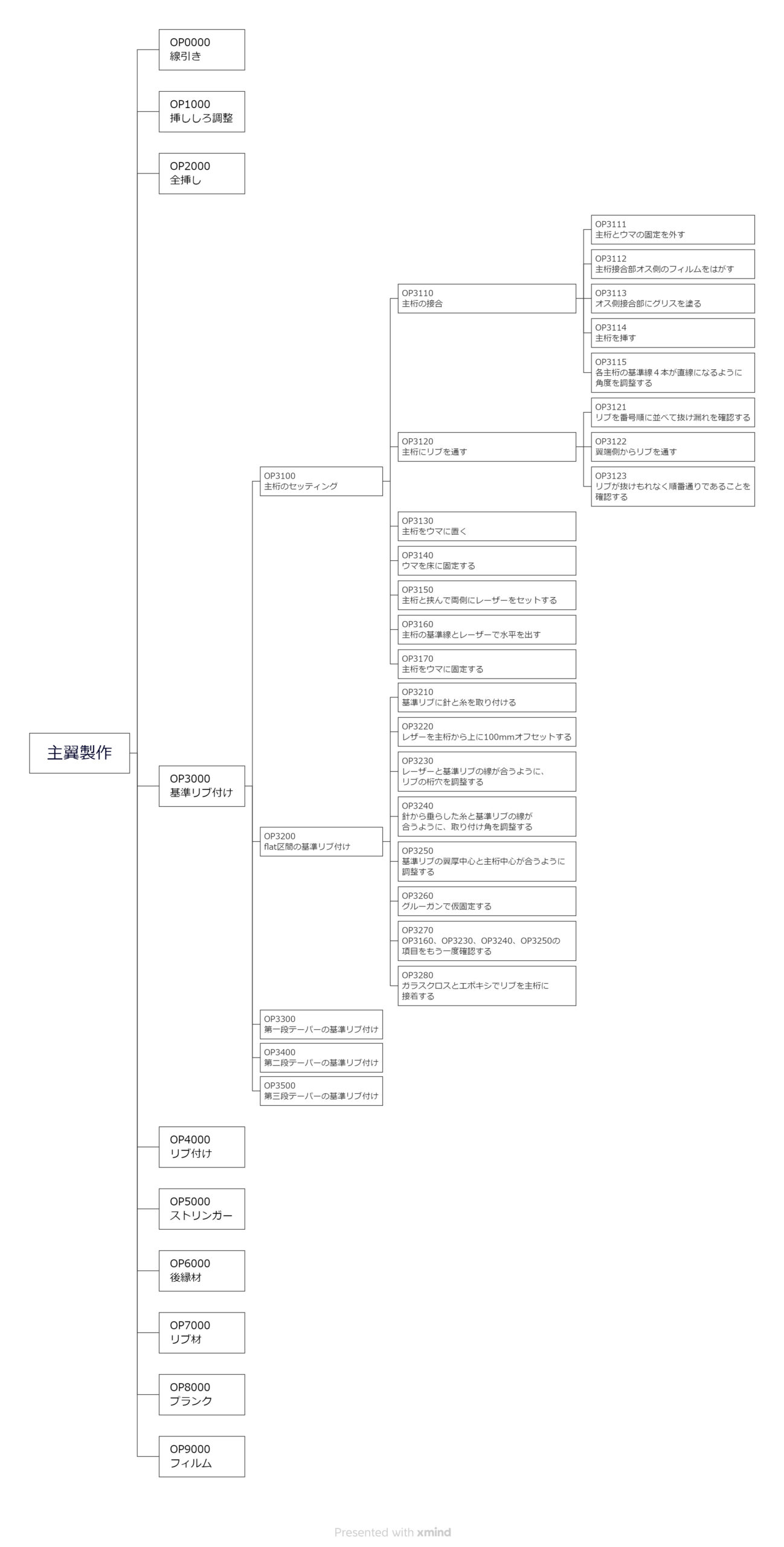
OPはOperation(工程)の略で、数字が小さい方から大きい方へと作業が進んでいく
OPxxxxの数字がとびとびになっているのは、上の図からもわかる通り大きな工程をより小さな工程へ分解していくためである
これまで何度も機体製作の引継ぎ資料を作ってきたが、今回ツリー形式で作ってみて、機体製作の引継ぎ資料としてはツリー形式の資料が一番わかりやすいんじゃないかと思った
正直これを最後まで完成させるだけでも凄まじい価値の引継ぎ資料になると思う
Structure tree
上記のように、製作工程は粒度が大きいものから小さいものまでさまざまな階層があり、どの階層のOperationをPFMEAの対象として選んでもよい
今回はProcess Flowの中で最も大きい粒度であるOPX000をProcess StepsとしてPFEMAを実施することにしたので、Structure treeは以下のようになった(クリックして拡大)
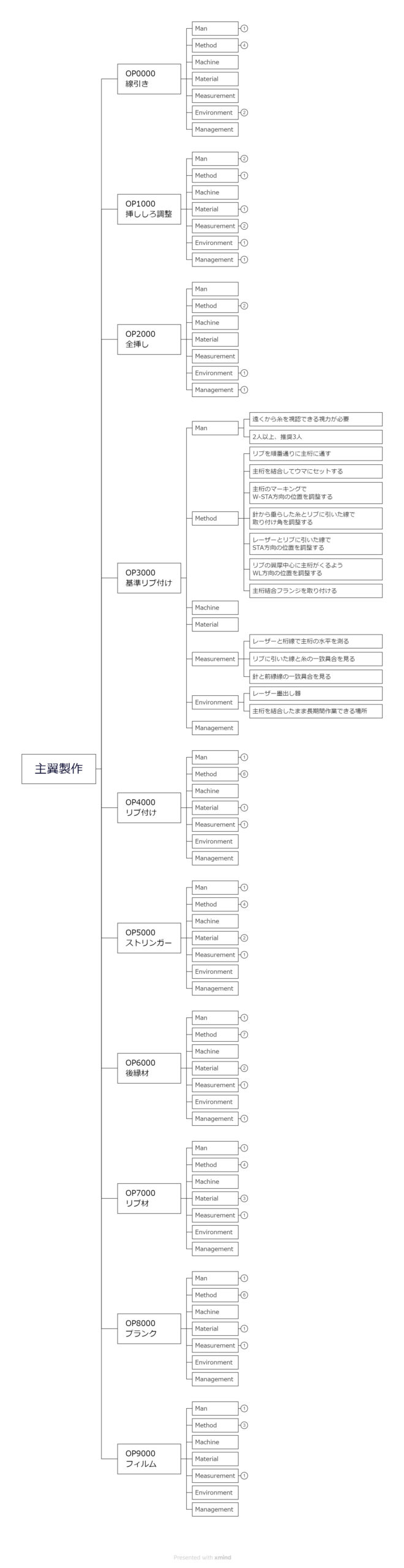
上の画像の3階層目(ManとかMaterialとか)までがStructure treeであり、4階層目の記述は次のSTEPで検討するProcess Functionと呼ばれるものになる
ちなみに今回はProcess Elementとして6M+Eを用い、以下のような定義で使用した
- Man: 作業に必要な資格、人数、スキルなど
- Method:作業方法、後片付けなどの製品性能に影響を与えない工程は除く
- Machine:NCや治工具など
- Material:接着剤や部品の材料など
- Mesurement:点検、検査の方法
- Environment:作業場所、換気の条件など
- Management:工程管理のための注意点など
STEP3: Function Analysis
STEP 3では以下のことを実施する
- Function treeの作成
function treeとは、前ステップで作成したStructure treeの各要素について具体的な記述(Process function)を加えたものである
このfunctionの記述は、動詞ベースの現在形で書くよう推奨されている(〇〇を××する)
Process Itemのfunctionでは工程全てが何の問題もなく完璧に完了したときの結果を記述する
- 例:部品を組み立てる
Process Stepのfunctionでは各工程の作業を具体的に記述する
- 例:蓋をボルトで取り付ける
- 例:配線を接続する
- 例:表面の塗装をする
Process Elementのfunctionでは各工程を成り立たせるために必要な要素について記述する
- 例:[Man] はんだ付けの資格を持っている
- 例:[Machine] NCの送り速度をxxにする
- 例:[Environment] 温度を25℃以下にする
Process Elementの設定についてはSTEP4と関わりが深いので、まずはひと通り記事を読んでみてほしい
これらのfunctionの繋がりを論理的に確かめるためには,以下の質問が有効である
- (トップダウン)上位の機能をどのようにして実現するのか(How?)
- (ボトムアップ)下位の機能はなぜ必要なのか(Why?)
この質問をすることで,function analysisの正しさや抜け漏れがないことを確認することができる
このような質問を駆使しつつ、できる限り抜け漏れのないfunction treeができればSTEP3は完了である
例: QX-20
今回はまず主翼のprocess flowを見ながら「それぞれの工程はなぜ必要なのか(Why?)」の質問を用いてボトムアップでProcess Itemのfunction(全ての製造工程が問題なく完了したときにどのような状態になっているべきか?)を考えた
その結果、鳥コン滑空機であるQX-20の主翼製作のProcess ItemのFunctionを次のように定義した
- 必要な揚力が発生するよう図面通りに主翼を製作する
- できるだけ抗力が生じないようなめらかに主翼を製作する
- スケジュール通りに主翼を製作する
ここをスタート地点として、今度は逆に「上位の機能をどのようにして実現するのか(How?)」という視点から主翼のProcess StepのFunctionおよびProcess Elementのfunctionについて考えていく
Function treeはこんな感じ
※今回使っているFMEA Tool(FMEA Studio Free)の制約上、12個までしか要素を追加できないので、Function treeはOP3000のみに対して作成した
Function Analysisを実施することで、主翼製作の各工程とそれらの構成要素、さらにはそれらの機能的なつながりが明確になった
STEP4: Failure Analysis
4つ目のステップでは以下のことを実施する
- Failure treeの作成
いよいよFMEAの軸となるFailure Modeの分析を始める
PFMEAにおけるFailuresは、STEP3で定義したprocess functionに対してそれぞれ定義される
Failure chain
それぞれの機能に対して設定した故障モードは、Failure chainによって繋がっている
Failure chainとは、ある注目している故障モードに対して、1つ上の階層の故障モードは注目している故障モードによる故障の影響(Failure effect)になっており、1つ下の階層の故障モードは注目している故障モードの故障の原因(Failure cause)になっている、という考え方である
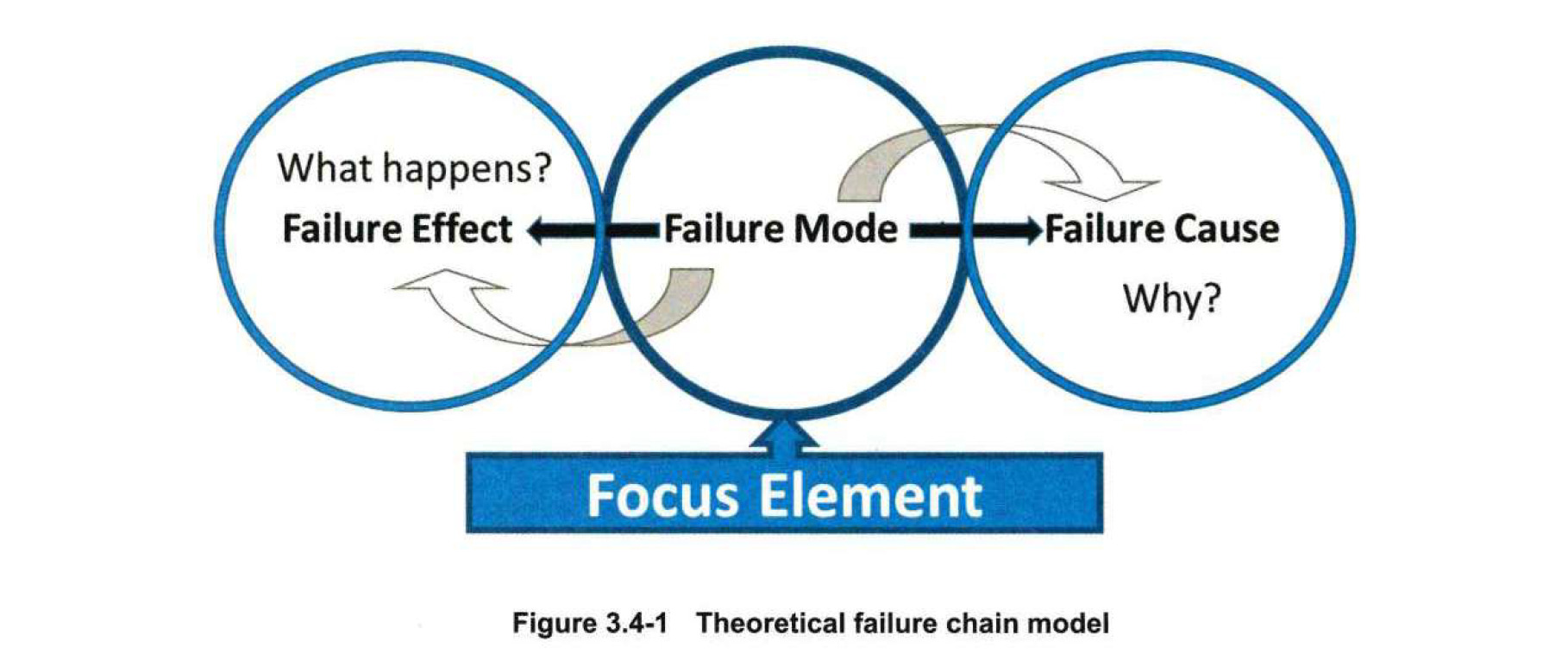
これにより、すべての故障モードに対して、何が原因で起こるのか、その結果どのような影響が出るのかを整理することができるようになる
Failure effect
Failure effectは、故障モードによってどのような影響が出るのかを記述したもので、以下の3つの観点から評価する
- 自工程への影響(Your Plant)
- 次のプラントへの影響(Ship-to Plant)
- 最終製品への影響(End User)
前のSTEPで設定したProcess Itemをそれぞれネガティブな方向に変換して考えるといい
Failure Effectについては例えば以下のようなものがある
Your Plant
- 次の工程に進めず製作がストップする
- 作りかけの部品が全てスクラップになる
- 膨大な修理や戻り作業が発生する
- 人手が足りなくなり長時間労働になる
Ship-to Plant
- 荷重試験の治具にセットできない
- 運搬用のトラックに入らない
- 大会会場で組立できない
End user
- 性能が下がる
- 使い勝手が悪くなる
鳥人間コンテストの機体製作だとだいたいのFailure effectがYour PlantかEnd userに分類されることになる
また、End Userに対するFailure effectは、DFMEAで分析されたFailure Modeと共通するものもある
Failure Mode
Failure Modeはそれぞれの製造工程においてどのような失敗が起こるかを記述したもので、以下のようなものがある
- 図面通りの製品ができていない
- 作業ストップ
- 表面の汚れ、キズ、凹み、破損
- 接合面の段差、隙間
- 識別忘れ、部品間違い
- 動作不良
ここらへんは前のSTEPで設定した各工程のProcess Stepに対して、蓄積した失敗集や引き継ぎ事項などから情報を持ってくることになる
ひと通り機体の製作を経験すればとめどなく溢れてくるんじゃないだろうか
Failure cause
Failure causeはProcess Elementに対して設定され、Failure Modeを引き起こす原因となるものである
上で抽出したFailure Modeに対して、4M、5M+1E、6Mなどの手法を用いてFailure Causeを分析していく
ちなみに、このような手法は製造業で用いられているフィッシュボーンチャート/特性要因図を作成する際にも用いられるものである
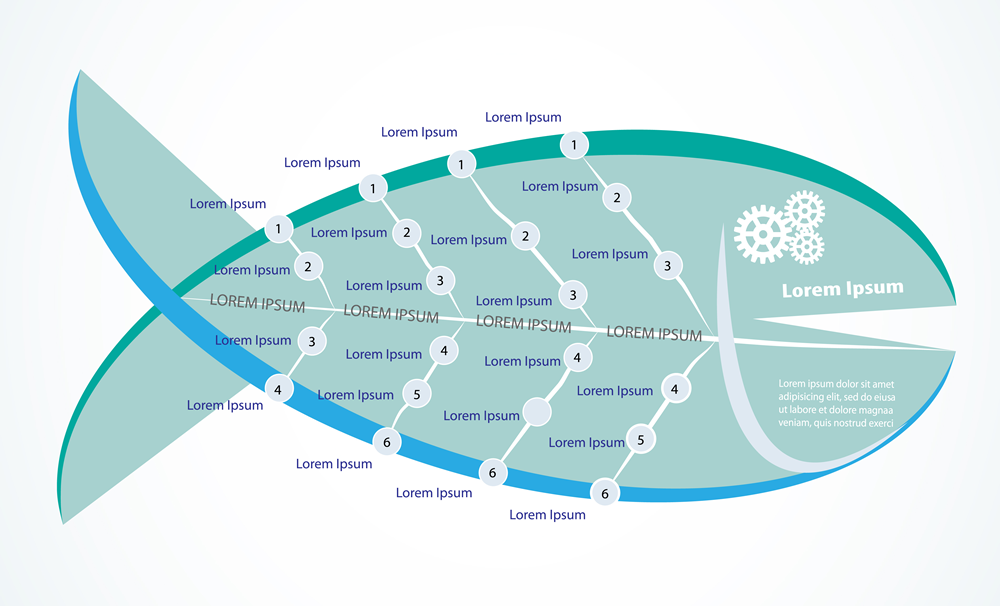
structure treeの各部品についての故障モードを列挙し、Failure chainで繋ぐことができればSTEP4は完了である
DFMEAとの関係
PFMEAのFailure Effectのうち、End Userに属するものはDFMEAのFailure Modeと共通になることがある
例えば、主翼のPFMEAのFailure Modeで「主翼の表面が凹みができる」というものがあったとすると、Failure Effectは「主翼の性能が下がる」となり、主翼のDFEMAのFailure Modeと共通のものになる。
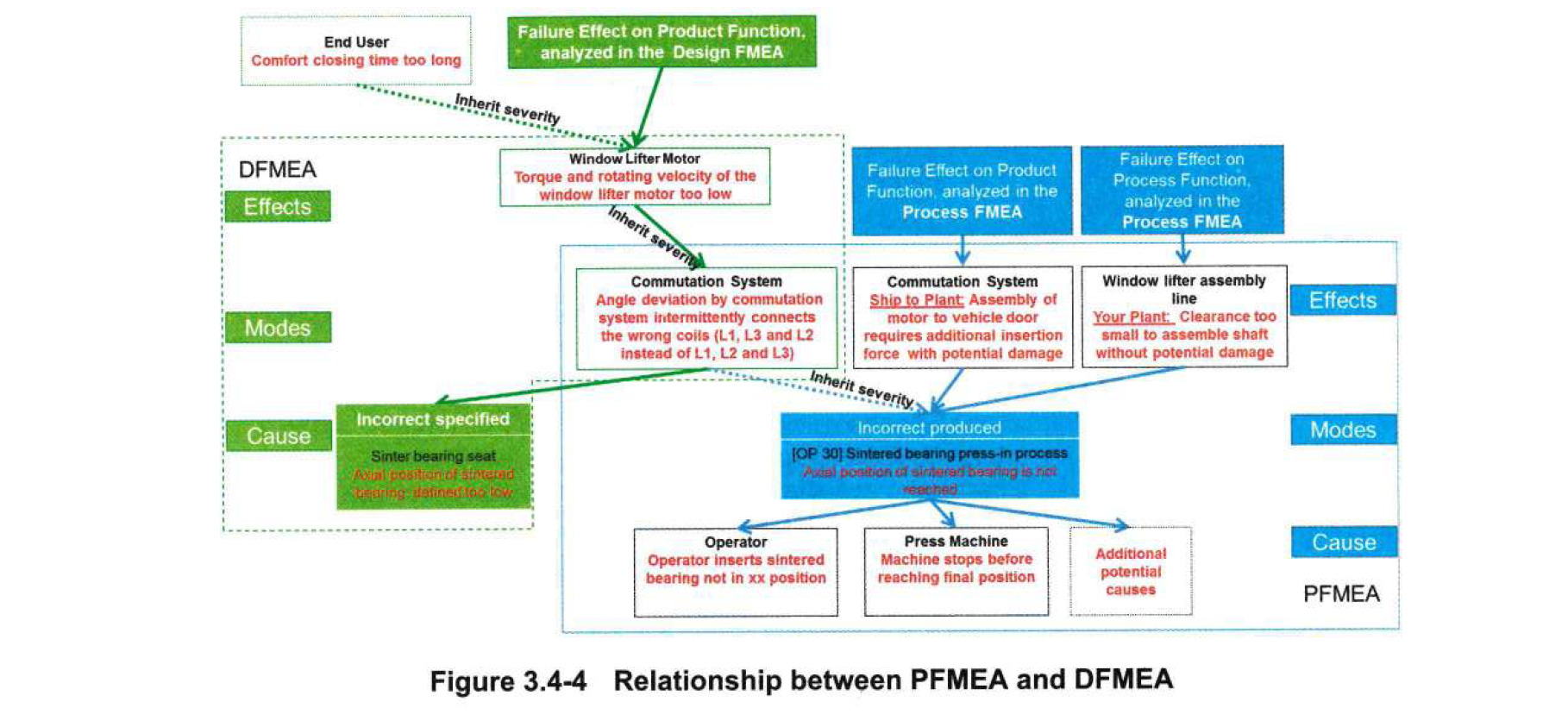
例: QX-20
QX-20のFailar Analysisはこんな感じになった
STEP5: Risk Analysis
5つ目のステップでは、以下のことを実施する。
- 評価マトリックスの作成
- Severityの評価
- Prevention Controlの調査
- Occurrenceの評価
- Detection Controlの調査
- Detectionの評価
- Action Priorityの計算
最終的には全てのFailure Modeに対してAP(Action priority)が設定されることになる
リスクの大きさを定量的に評価し、APによって対策の優先順位をつけることで、限られたリソースの中で最大限の改善効果を発揮することができるようになる
それでは順番に説明していく
評価マトリックスの作成
FMEAでは、リスクの大きさをSeverity(S)、Occurrence(O)、Detection(D)の3つの観点から、それぞれ10段階評価で定量的に評価する
Sは故障モードの深刻さ、Oは故障モードの発生頻度、Dは故障モードの検出性である
これら3つの指標を組み合わせることによって、いろいろな故障モードを表現することができるようになる
- 非常に深刻だが、ほぼ発生することはなく、発生したとしても容易に検出できる故障モード(注意しておけば問題ない)
- 深刻さは中程度だが、それなりに発生し、ほぼ検出できない故障モード(毎回流出して問題になる)
- 深刻さは低いが、高い確率で発生し、検出は容易な故障モード(やり直しが発生してスケジュールが遅れる)
リスクを10段階評価する際は、FMEA実施者によって評価がばらつかないように、評価マトリックスを作成する
VDA FMEAのハンドブックにもマトリックスは載っているが、自動車産業用なので、自分たちが作るものに対して修正する必要がある
例: QX-20
今回は鳥コン滑空機を題材にしてリスクマトリックスを作成してみた
Sのマトリックス
PFMEAのSのマトリックスは、Your Plant、Ship-to Plant、End Userそれぞれについて作られる
今回はYour Plantのみ新たに作成、鳥コン滑空機はどこかに納品するものではないのでShip-to Planについては適用外、End UserについてはDFMEAのSのマトリックスと共通のものにした
Your Plantについては、問題が発見されたときの修理所要時間をベースにリスクの大きさを設定した
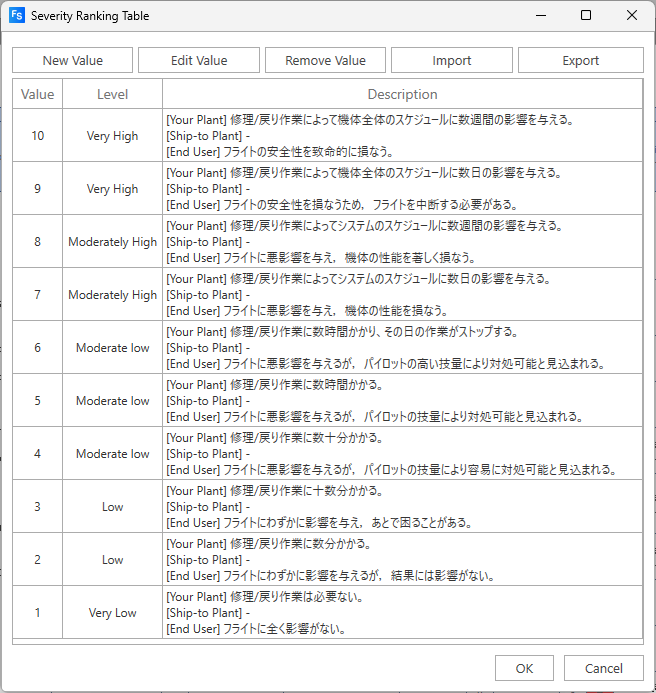
Oのマトリックス
Oのマトリックスで評価するPFMEAの故障モードの発生頻度は、Prevention Control(後述)の効果の高さで評価される
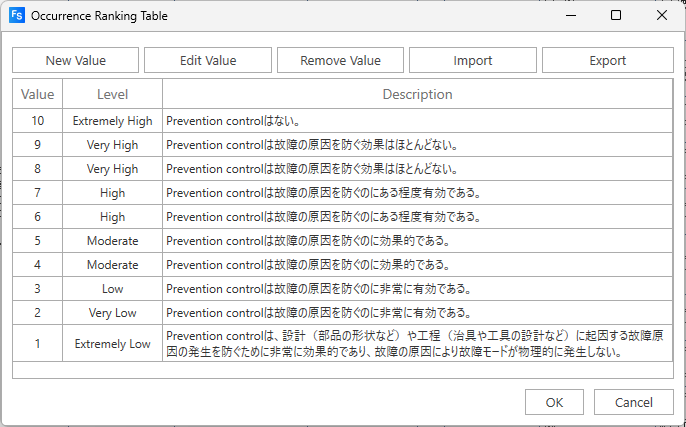
Dのマトリックス
Dのマトリックスは製造工程で発生する故障モードの検出性を評価する
要するにチェックして見つかるかどうか、そしてそのチェックの方法の信頼性が高いかどうかである
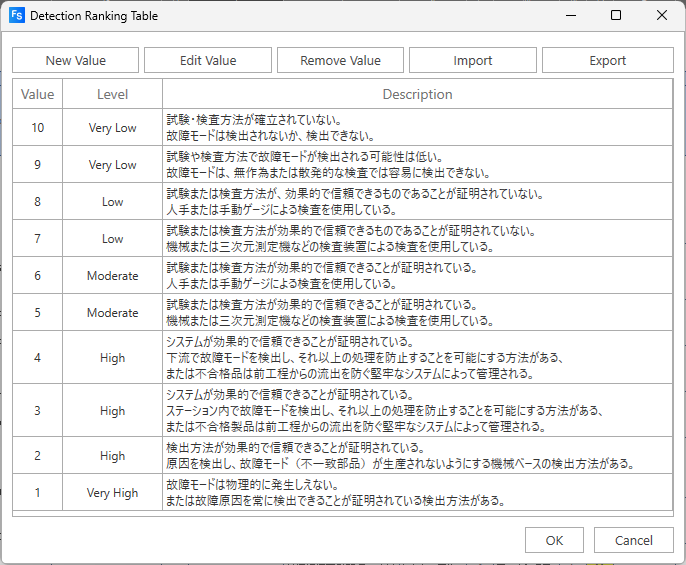
3つの評価マトリックスが揃ったら、いよいよリスクの評価を行っていく
Sの評価
S(Severity)の評価は、その故障モードに対するFailure effectに対して行われる
故障モードによって引き起こされる製品への影響の深刻さを、上で作成した評価マトリックスを用いて10段階で評価する
故障モードがシステムへ与える影響であるSの評価は、基本的に変わることのない普遍の値である
たとえ工程を変更してフールプルーフを組み込んだりしても、改善されるのはOの値やDの値であり、もし万が一製造ミスをしてしまった場合のFailure effectの深刻さは変わることはない
Prevention Controlの調査/Oの評価
Oの評価を実施するために、現在実施しているprevention controlを調査する
prevention controlとは故障モードの発生確率を下げるための予防措置であり、PFMEAにおいては以下のようなものがある
- 片手じゃなくて両手で作業する
- ポカヨケを使う
- そうとしか取り付けれないような形状にする
- 治工具の点検をする
- 手順書を作る
- 作業者の教育をする
ここでは「これからやろうとしていること」ではなく、「いま既にやっていること」を記述する必要がある
「これからやろうとしていること」はSTEP6で記述することになっている
調査したprevention controlに対して、評価マトリックスをもとにOの評価を実施する
Sの評価とは異なり、Oの評価はprevention controlの見直しや設計の変更によって改善することができる
Detection Controlの調査/Dの評価
Dの評価を実施するために、現在行なっているdetection controlを調査する
PFMEAにおけるdetection controlとは、製品製作後に行うチェックや検査のことで、以下のような種類がある
- 目視検査
- サンプルと比較する
- 定規で寸法を計測する
- トルクを測る
これらの検査やチェックをすることで、万が一製造ミスがあった場合でも次の工程に進む前にミスを発見し、修正することができる
Action Priorityの計算
S、O、Dの評価を入力すると、AP(Action Priority)が自動的に計算される
APはSODの組み合わせで以下のように決定される
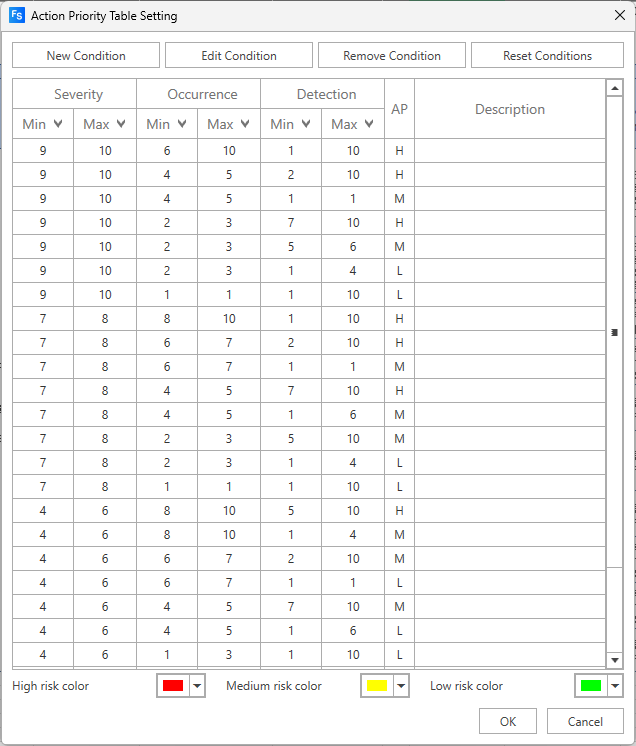
似たような指標であるRPN(Risk Priority Number)が単純なS×O×Dの掛け算であるのに対して、APはSにより重みづけをしているのが特徴である
重みづけにより、Sの値が大きい項目はOやDが小さい値でもAPが大きくなるように設定されている
例: QX-20
QX-20の主翼についてのSOD評価は以下のようになった
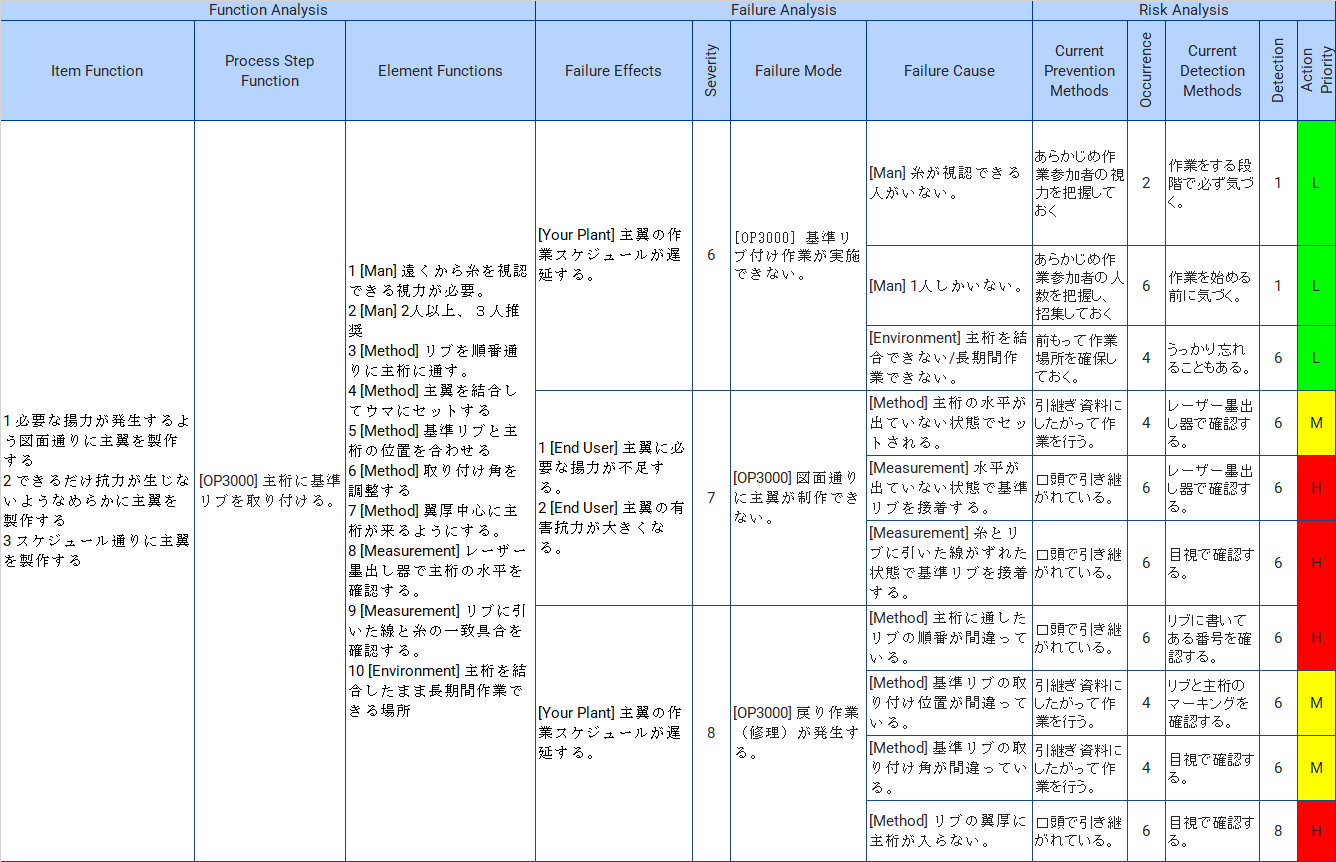
Sの評価
主翼は機体の安全性や性能に大きな影響を及ぼすため、全体的にSの値は大きくなっている
Your Plantについては、その日の作業が止まる程度の故障モードと基準リブ付け直しが必要になる程度の故障モードがあり、それぞれSの値は6、8とした
基準リブ付けの作業においては一撃で全体スケジュールが崩壊するレベルの故障モードはなかったが、例えば荷重試験の手順ミスで主桁が折れたり、電装の作業ミスで回路がショートして基板を焼き殺したりするような故障モードの場合はSの値が9や10になるかもしれない
End Userについては、DFMEAのリスク評価にならってSの値を7としている
Oの評価
prevention controlは、おおむね作業の引き継ぎ資料を使ってそれ通りに作業することが基本になる
今回のOの評価については、引き継ぎ資料が存在するものを4、口頭でしか伝えられていないものを6とした
ややリスク評価が厳しすぎるように感じるかもしれないが、口頭での伝承が実行される保証などどこにもないし、引き継ぎ資料を作ったとしても、後輩がそれを読んでその通りに作業してくれるとは限らない
processのリスクを減らすためには、然るべき作業資料を読んでその通りに作業することを保証することが必要になる
必要な作業資料を過不足なく読んでもらうためには、作業に必要な資料の一覧などを準備しておけばよいし、新入生用、班配属直後用、班長用、などとリストを作っていけばそれがサークルの教育シラバスとして機能するようになる
引き継ぎ資料についても、資料の中でProcess flowのようなものを示して作業の抜け漏れをなくすとともに、実際に作業する際に使用できるチェックリストのようなものを作成しておけば、全ての作業が問題なく実施されたことを第三者が確認できるようなる
ここまでやっておけば、故障モードのOの評価を2とかにしてもいいと思う
Dの評価
鳥人間の製作に対するチェック作業は手動で行われることが多いので、評価は一律で6となった
もちろんチェックする担当者の間で基準についての目合わせはしているものの、人間である以上多少のばらつきや見落としは起こりうると考えられる
もう少し技術が発達すれば、スマホで3Dスキャンして寸法の精度を確認したりできるようになるかもしれない
APの評価
SとDの大きさはどれも同じくらいなので、Oが大きい故障モード(口頭でしか伝承されていない工程)のAPが大きくなっている
特に、確認やチェックの作業はそれ自体やらなくても機体としての形が一応できてしまうので、非常に抜け漏れが起こりやすいと思う
このように、故障モードの一覧とそれに対応するAPの値を示すことで、これから製作方法を考える人やその人の指示に従って作業する人に対しても、わかりやすく定量的に「外してはいけない製作の勘所」を伝えることができるようになる
つくづくFMEAは引継ぎ資料として有能である
これでSTEP5は完了してので、次のSTEPへと進む
STEP6: Optimization
STEP6では、以下のことを実施する
- Mitigation Actionの設定
- リスクの再評価
STEP5によって、故障モードの一覧とそのリスクの大きさおよびAPが得られたので、APの大きさに従ってリスクを低減させる対策(Mitigation Action)を設定していく
上述のとおり、Sの値はFailure effectに固有であり変わらないものなので、Mitigation ActionはOの値を下げるかDの値を下げるかのどちらかになる
また、APの低いものについてはMitigation Actionの設定の必要はないため、「対策不要」とでもコメントしておけばよい
対策を設定し、担当する人とその期限を決定したら、Mitigation Actionを実行する
Mitigation Actionの実行結果をもってODの値を再評価し、APの値が下がれば対策は完了である
QX-20
例えばQX-20では以下のようになった
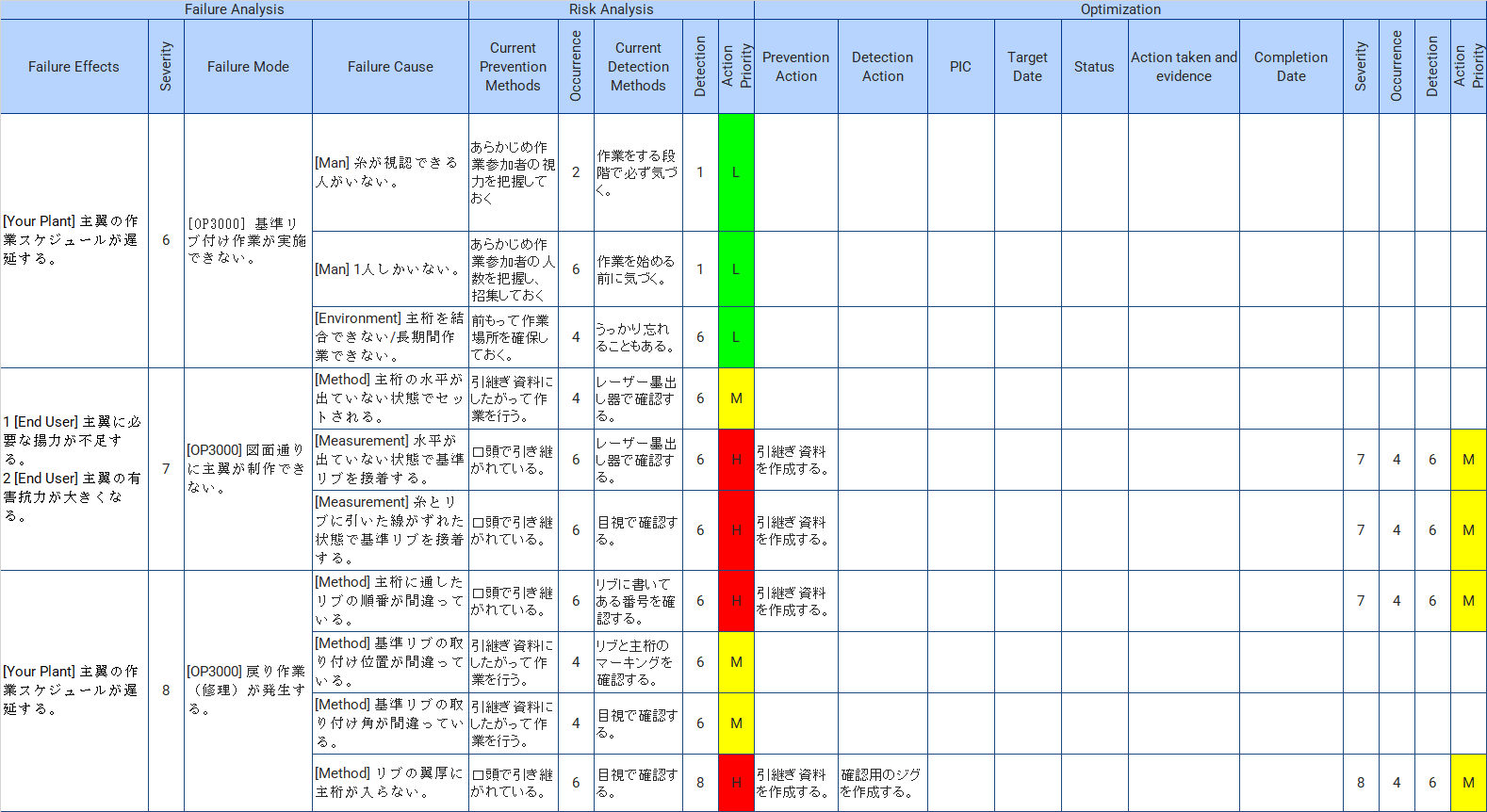
今回の例では、APがHighの故障モードのみ対策を設定し、それ以下の故障モードは対策不要とした
このように、APを設定することで、順序立てて対策を検討することができるようになり、限られた時間や人員のリソースを最大限に有効活用することができる
1年間という短い期間の中で設計、製造、試験、運用を行う必要のある鳥人間のような過酷なプロジェクトにおいて、許容できるリスクと許容できないリスクを定量的に識別できるのはかなりアドバンテージになるのではないかと思う
また、引き継ぎのためにPFMEAを実施した場合は、STEP5のRisk Analysisまでを上の代が実施し、STEP6から下の代が引き継ぐというやり方もできる
STEP7: Results Documentation
STEP7では、以下のことを実施する
- PFMEAの結果の文書化
正直これは各チームのチーム運営の方法に大きく依存するので、好きなようにやればいいと思う
もちろんこれまで説明してきたBOMやPFMEAのファイルだけでも十分に素晴らしい資料だと思うが、追加で以下のことくらいはまとめておいてもいいかもしれない
- PFMEAをやった目的/意義
- 対象を選んだ理由
- チームでFMEAをレビューしたときの議事録
- 実際にFMEAをやってみた感想
- 本番の結果を振り返って
以上でVDA FMEAの7つのSTEPは全て完了である
DFEMAの手順
おわりに
ものづくり系サークルに所属する学生のために,自動車業界の国際規格IATF16949をベースとしたVDA FMEA(PFMEA)についての説明を行った
PFMEAのそもそもの目的に「体系化した知識の蓄積」があるので、PFEMAという枠組みは学生モノづくりチームにとても適しているように思う
コメント